Finishing methods for die-casted products
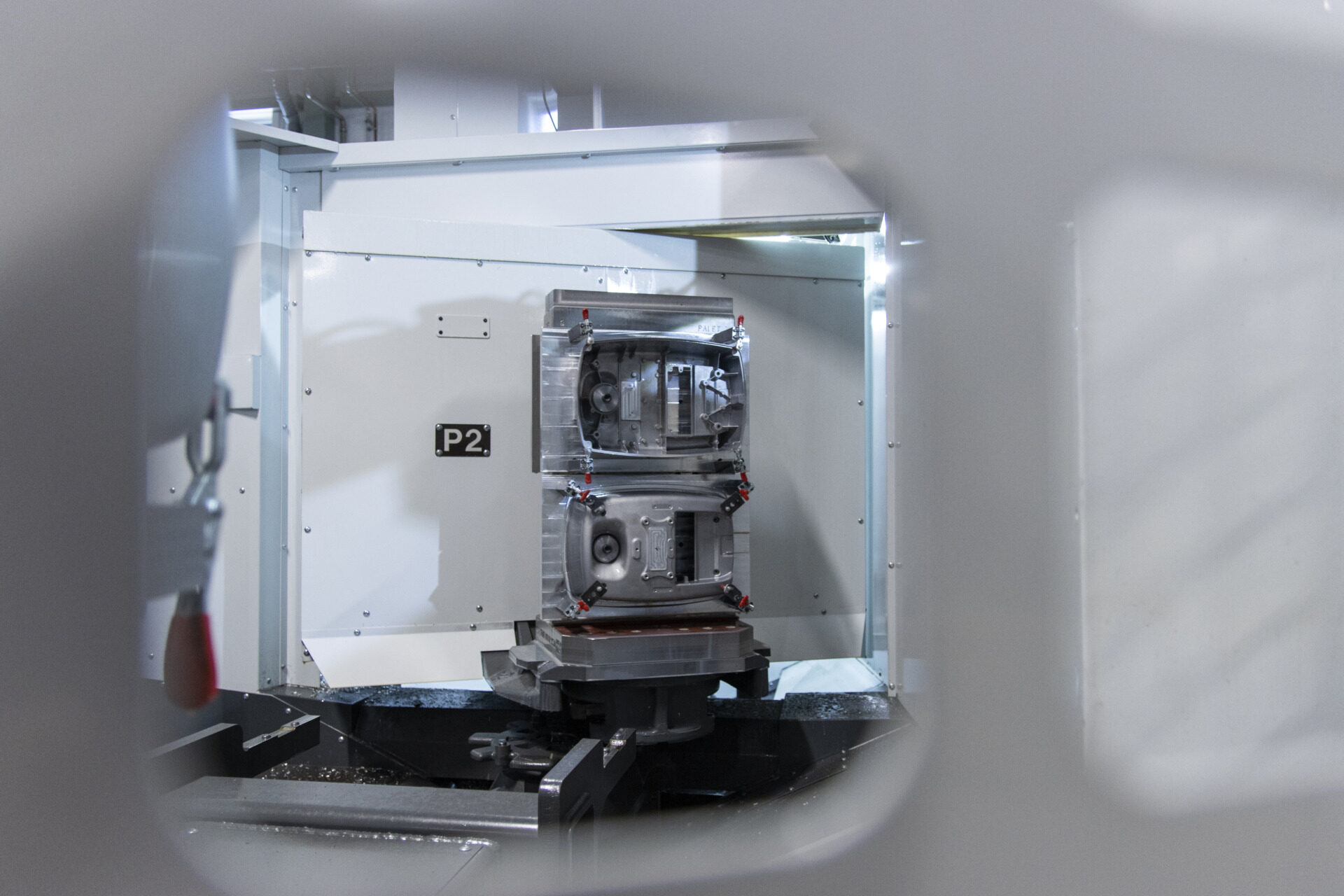
The finishing of die-casted products and components is an important stage in the production process. Finishing stages influence the functional and visual quality of the product.
Why choose Ouneva Group for finishing?
We offer a diverse selection of different finishing options. The broad technology portfolio of our group enables us to offer the manufacturing and all the processes, including finishing, in-house. To our customers, this means competitive operations and smaller risks regarding their supply chain. Our experts are keenly aware of what our units can offer as a group, which means we can guarantee professional and solution-oriented service. Our experience in manufacturing die-casted products spans over more than 30 years.
Why finish a product? Doesn’t it only mean more costs?
In the manufacturing of die-casted products, the finishing stage is usually mandatory without exceptions. In the casting process of the product, some kinds of marks usually appear on the product due to the ingates, ejector pins and vent outlets of the mould. In the design stage for the product and the mould, unnecessary holes and cavities of the product are always minimized to create as little burr as possible. Deburring is a necessary finishing step, so the responsibility of reducing other finishing steps is one the design stage.
If surface treatment, such as powder coating, is desired for the product, the surface must be prepared for the treatment. Fundamentally, most of die-casted items are powder coated or surface treated to avoid the oxidization of the surface that leads to weakening of the visual and functional quality. Material choices can reduce the need for powder coating, and when deciding on the materials, the end usage environment of the product has to be taken into consideration. Before coating or surface treatment, the product is usually prepared by shot blasting or vibratory deburring. More information on these methods is in the end of the article.
The finishing stage of die-casted items is a so-called “necessary evil”, but with careful mould and product design, the requirements and related costs can be reduced. The requirements for finishing the product are also defined by the usage environment. For example a product, that has to visually of very high quality, but is used in indoor environments only, is finished in a different way than a product that is used in challenging conditions. The functional requirements of the product also influence the finishing requirements.
What do the costs consist of and how to control them?
The needs for finishing an item can be reduced significantly in the mould and product design stage already. A good product designer takes different mould-related aspects into account with the finishing stage in mind. For example, hiding ingate openings on surfaces that are not functional or visual decreases the need for finishing. So again, the decisions made in the design stage influence the total costs of the manufacturing in all its stages! Our DFM-experts are always ready to answer any questions you have in mind, so please don’t hesitate to be in touch if questions arise.
We discussed vacuum-assisted die-casting in more depth in an article about die-casting. Vacuum-assisted casting reduces the need for finishing, due to better exiting of gases during the casting process. The mechanical and visual quality of the item improve because of the more efficient gas extraction. The vent outlets are also considerably smaller in a vacuum-assisted die-casting mould, which in turn means less marks to finish.
Material choices influence the whole manufacturing process, so we truly recommend you to discuss the most suitable choice for your product with your foundry. Different material alloys are numerous, and the most suitable choice is often the alloy, that fits into the end usage environment as well as fulfils the requirements of the functional properties. Different ratios of ingredients in the alloy influence the functionality and quality of the product. For example, AlSi10Mg is an alloy with great resistance to corrosion. AlSi9Cu3 on the other hand is a little less pricier than the beforementioned, but the resistance to corrosion is slightly worse. This means that a small difference in material price might influence the costs related to the finishing process.
The expertise of your chosen foundry also has an impact on the overall costs of your product. Naturally, the more experienced and professional your foundry is, the easier it will be for you to find out what is the best possible manufacturing process for your product.
Options for finishing your die-casted product at Ouneva Group
Machining
For machining, we have both horizontal as well as vertical machining centres. For larger volumes, we can use a 6-station machining centre that can automatically handle all kinds of items. Robots are taking care of most of the product handling in our facilities. The machining procedures often done on die-casted items are drilling, threading and creating flat surfaces by milling. Our machinery is modern and our machining experts react quickly to our customers’ inquiries.
Grinding
Grinding is normally done to products prior to powder coating or surface treatment, to create a clean visual surface that promotes the stickiness of the coating. Automated grinding units bring efficiency and uniform quality into our processes. Automation solutions enable us to handle large volumes smoothly and cost-efficiently. In addition to entire grinding units, we also provide other flexible grinding solutions with different tools, such as machine files.
Shot blasting
Shot blasting is done in cabinet-shaped blasting machines, where we can handle multiple products in one run. In shot blasting, small stainless steel shots or sand is blasted with high velocities into the surface of the product. This cleans up the surface and creates a smooth structure on it. Shot blasting is done for products before powder coating. Because of the structure the process creates on the surface, paint sticks to it better. Shot blasting also removes burr and slightly rounds off sharp edges.
Vibratory deburring
Vibratory deburring is also used to prepare the surface of a product for powder coating. Vibratory deburring is done to multiple products simultaneously, which means the process is more efficient. We have bowl and tub-shaped continuous flow deburring equipment in use. In autumn 2022, we are investing into a new continuous flow line for our facilities. During the process of vibratory deburring, the items and the tumbling media roll and tumble around a vibrating container. The tumbling media defines the structure of the shape and the amount of deburring that occurs during the process. We offer multiple choices for the tumbling media, and we gladly help you to choose the best one for your requirements. In addition to preparing the surface for powder coating, vibratory deburring is also used for rounding sharp edges and to remove the burr, like the name suggests.
Powder coating
Powder coating is the finishing touch to the visual outcome of the product. Depending on the product, we powder coat items either on our automated coating lines or do it manually by our experts. Powder coating gives the item an extra layer of resistance to corrosion and wear. For die-casted items, we have carefully chosen the most suitable pre-treatment agents and the plastic powders, that are used in the process. If you’re not sure about what agents suit your products the best, ask us and we will assist you. Sometimes, there is no need to powder coat the product, but the additional protective layer against oxidization is desired. In that case, coating the product with only the pre-treatment agent might be a good option. We use Bonderite and Surtec, that both protect the surface efficiently, but do not change the visual outcome of the product significantly.
Anodizing and other options
In addition to the beforementioned methods for surface treatment of die-casted products, we also offer more special methods, such as anodizing and passivating and nickel plating for zinc items. Anodizing is done on aluminium items to improve the resistance to corrosion. Anodizing also gives the item a distinct visual surface and resistance to wear. Anodizing functions as an electrical insulator. It can be used as a pre-treatment for powder coating, since it provides the paint powder added stickiness and corrosion resistance. Passivating and nickel plating are done on zinc items to provide resistance to corrosion and to create an impressive visual outlook. Different plating processes can be done on our automated surface treatment line. We gladly help you with choosing the most suitable surface treatment option for your products, and we always encourage you to carefully consider the requirements of the end usage environment!
We also offer sealing services. Sealing can be done on the item to reach certain standards for humidity or dust protection or as an EMI seal. An EMI seal means that the sealing provides good electrical conductivity and interference protection between the items. We can seal items up to IP65 class.
To finish it off
Options are numerous, when choosing the best finishing method for die-casted products. To control the lifetime costs of the product, the needs for finishing should be taken into account already in the product design stage. That enables you to optimise the amount and efficiency of the finishing processes in the most suitable way for your product. Automated processes and the expertise of the foundry are the important factors to keep in mind, when choosing your die-casting partner. We assist you gladly in finding the best solutions!
If any questions arise, we help you out gladly. You can contact us here.
More about die-casting as a manufacturing method here.