Protecting electronics – why and how to safeguard sensitive products?
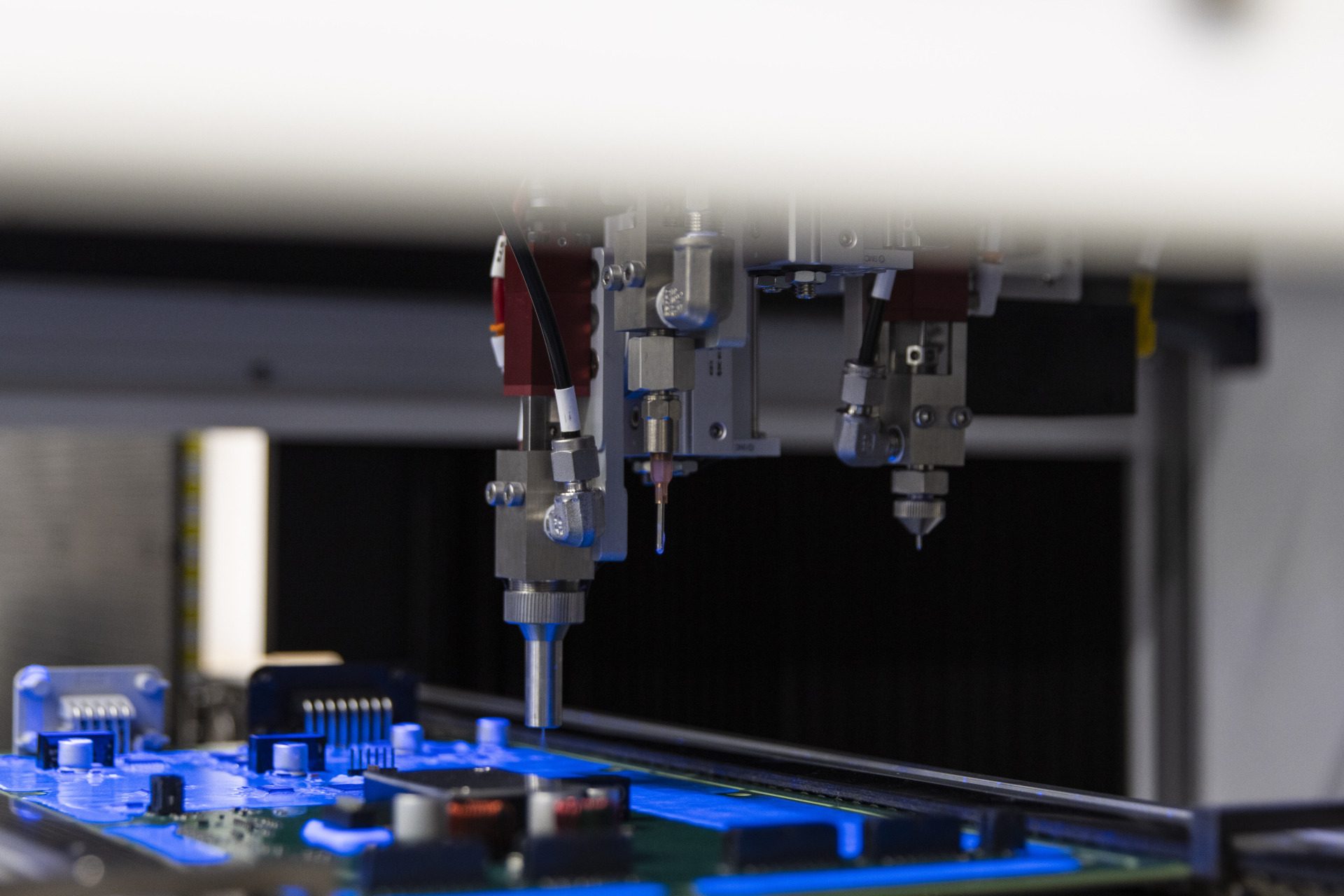
Protecting electronics is a crucial step in the manufacturing of electronic products. Sensitive components and circuit boards require protection, particularly when the final product is used in demanding conditions. Electronics protection extends the product’s lifespan and reduces the risk of malfunctions. It shields against various external factors, such as environmental conditions and mechanical impacts.
Why is electronics protection important?
Electronic devices, and nearly all equipment that keeps our society functioning, contain some form of electronics. The increasing volume of electronic devices is reflected in statistics on electronic waste. Poorly protected electronics often end up as waste, so environmental considerations should also be taken into account when designing protection strategies.
Electronics protection prolongs a product’s service life. High-quality protection reduces the risk of short circuits, corrosion, and other damage caused by environmental factors to circuit boards and components. Protection also enhances the reliability of electronic products, ensuring they function properly even in extreme conditions. Measuring instruments, medical equipment, and defence technology are examples of applications where any malfunction is unacceptable. Proper and high-quality electronics manufacturing, including protective measures, ensures functional devices for demanding applications.
What can damage electronics?
As the packaging density of electronics increases, electronic devices become more sensitive to various environmental factors. The most common factors that can damage electronics include:
Moisture: Causes corrosion, leading to leakage currents and even short circuits.
Contaminants: Can cause malfunctions in the product and, like moisture, lead to leakage currents and even short circuits.
Chemicals: May cause long-term damage, leading to malfunctions.
Mechanical stress and vibration: Can cause components to detach or break.
Heat: Can damage components.
Some of these risks can be mitigated during the product’s design phase. However, environmental factors remain beyond the designer’s control, making high-quality protection essential for preventing such failures.
How are electronics protected?
There are various methods for protecting electronics. The choice of method depends on the product’s usage environment, as well as the structure and size of the circuit board. Below are the most common protection methods, including those used at Ouneva Group:
Parylene coating
Parylene coating is a specialty at Ouneva Group. We were the first electronics contract manufacturer in Finland to adopt this technology. Parylene coating is applied in a vacuum chamber, where vapour deposition creates a polymer film on the product’s surface. The thickness of this film can range from 0.5 to 100 micrometres, depending on the product’s intended environment. Parylene coating is completely uniform in both thickness and coverage, whether on flat surfaces or around the edges of circuit boards and components.
This transparent, thin coating allows for visual inspection of the circuit board throughout the product’s lifecycle. Due to its biocompatibility, parylene coating is an excellent choice for medical devices. It is also highly durable, expanding the potential applications of protected products.
Potting
Potting involves encapsulating electronics with a 2K compound in an open enclosure. This process is automated, making it well-suited for large production volumes. The potting compound provides comprehensive protection against environmental factors and dampens vibrations.
Potting is ideal for demanding applications where the electronics are exposed to significant environmental stress or movement. While potting is slightly more expensive than methods like conformal coating, it offers superior protection. However, the added material increases the overall weight of the product, making it unsuitable for applications requiring lightweight solutions.
Low-pressure moulding
Low-pressure moulding is an effective protection method for sensitive products. The process takes place in a closed mould, where the material completely encapsulates the product. As the name suggests, the moulding is performed at low pressure, preventing damage or displacement of components.
Low-pressure moulding is commonly used to protect sensors and cable connections exposed to vibration or environmental stress. It can also be used to protect standard circuit boards when required by their usage environment. The hot-melt material used in low-pressure moulding offers excellent chemical resistance and provides full insulation. However, when selecting this protection method, the cost of the mould must be considered. Once the mould is in place, the process is efficient in both production time and cost, making it ideal for large-scale manufacturing.
Enclosures
Most electronic products are enclosed simply to integrate electronics within the product’s functional or external housing. However, enclosure design should take the product’s intended use into account. For example, products designed for outdoor use often require specialised sealing methods. Sealing is typically applied directly to the enclosure’s sealing surface using PUR material or silicone. The level of sealing is classified according to the product’s IP rating.
Conformal Coating
At Ouneva Group, conformal coating is applied to assembled circuit boards either manually or through automated processes. Various types of coatings are available, with the most commonly used being acrylic-based and urethane-based coatings.
Acrylic coatings are cost-effective and suitable for general protection. They offer high dielectric strength, as well as fair moisture and abrasion resistance, but are not ideal for applications requiring strong chemical resistance.
Urethane-based coatings provide better chemical resistance than acrylic coatings. They are also highly durable and moisture-resistant. However, urethane coatings are difficult to remove, making circuit board repairs challenging.
We have recently invested in a selective coating machine for our production, allowing the protection phase to be carried out efficiently. The automated system primarily uses acrylic-based coatings.
Top tips for electronics protection
The choice of protection method should be based on the product’s design, circuit board component density, and intended usage and environment. It is beneficial to consider protection strategies as early as the design phase to avoid challenges or failures during production.
During the prototyping phase, different protection methods can be tested. Before commencing mass production, it is crucial to determine the most suitable protection method. Sometimes, the best method is identified through collaborative testing with the customer.
Summary
Electronics are protected against external factors such as environmental conditions and mechanical impacts. Sensitive components must be safeguarded to prevent malfunctions, and high-quality protection extends the product’s lifespan. Selecting the right protection method is essential and should be based on the product’s design, purpose, and environmental demands.
Our experts are happy to assist in choosing the optimal protection method.
More information about the electronics manufacturing services we offer here.